8 Innovative Industrial Insulation Solutions
At its core, industrial insulation is the same as the insulation in your attic at home. It reduces transfer of heat to make a space more comfortable and cost less to maintain. Whether it protects against heat, reduces sound transfer, or protects against specific electromagnetic frequencies, industrial insulation works via the same basic principles. That said, the wider variety of tasks and environments for industrial application make industrial insulation more flexible, come in more varieties, and honestly more interesting than the fiberglass batting that’s over your head right now. Industrial engineers view insulation as a way of solving problems. For example, the insulative layers in a space suit solve the problem of astronauts freezing to death in -250F or burning up at +450F. A blacksmith’s apron is a lower-tech version of the same thing, designed to allow a blacksmith to stand closer to the forge to produce higher-quality work. Let’s look at some other problems industrial insulation solves today:

- Cryogenics Must Insulate Against High Temperature Extremes The whole point of cryogenics is to cool an object to well below the ambient temperature, and physics works against keeping that super-cooled object cold. Multi-layered insulation using low-emissive films, usually made with aluminum (3% emissive), copper (2% emissive), or gold (2% emissive), slow the transfer of heat to reduce the cost of maintaining the target temperatures. Of the common metals, aluminum is the cheapest but corrodes easily in oxygen, high humidity, and when exposed to most corrosive chemicals. Gold is non-reactive and highly corrosion resistant, allowing it to maintain its emissivity regardless of what it comes into contact with. Copper splits the difference, being slightly more expensive than aluminum and not quite as corrosion resistant as gold.
- Machinery Must be Insulated for Safety and Efficiency
- Temperature-Sensitive Tanks Must Be Handled With Care Liquids and gases are temperature sensitive and can be highly volatile. If they are warmed to temperatures too high, or too quickly, the results can be catastrophic. Tank insulation is typically made from a non-flammable bulk insulation like fiberglass or rockwool, but the most efficient insulations for this application include jackets of bulk insulation wrapped in a low emissive aluminum foil (3% emissive), addressing conductive and infrared radiant heat. These products working together address both conduction and radiation heat transfer allows the final insulation product to be as thin and lightweight as possible without sacrificing performance.
- Insulating Hot Pipes Improves Safety and Efficiency Whether you have cold pipes you need to prevent from warming, hot pipes you need to prevent from cooling, or pipes in outdoor climates you need to prevent from freezing, choosing the right insulation is key. While pre-formed foam pipe wraps are cheap and easily available, they are not the most efficient. For hot pipes where minimizing heat loss is key to equipment efficiency, the preferred alternative is a reflective insulation system. Using three or more layers of metal foil separated by small, sealed air spaces virtually eliminates conduction, convection and even heat radiation. The two most common metals for this application are aluminum and stainless steel. Aluminum foil insulates better with an emissivity of 3%, while stainless-steel has an emissivity of 25% and is resistant to atmspheric corrosion.
- Cooling Ducts are Under-insulated and Absorb Radiant Heat Cooling ducts running through a warm space don’t have the same level of insulation as the walls and roof of your structure. Building codes only require the ducts to be insulated to R-6 to R-8, while the ceiling should be insulated to R-38 to R-60, depending on the climate. In a hot climate, the air conditioning pushes the cold air through the under-insulated ducts sitting up in the hot attic, which results in hot air blowing through your vents before your AC has a chance to cool it down. Additionally, the cold air running through those ducts is subjected the outside heat radiating in, even if the ducts are perfectly sealed. Wrapping the ducts with reflective insulation, like a metalized aluminum (4-5% emissive) or a metalized copper (2-3% emissive) film laminated to an insulating substrate, like bubble insulation, flexible foam, or fiberglass, can reflect away the incoming radiant. This keeps the building comfortable for a fraction of the cost without such treatment.
- Noise Pollution is Hazardous to Industry Industrial spaces are often loud. Even if it’s not loud enough to get complaints to the zoning office, the decibels can impair communications, make your site less pleasant to work in, reduce workplace safety. Installing acoustic insulation usually consists of filling wall, ceiling, and floor cavities with a bulk insulator like high-density fiberglass or foam. Specially designed acoustic ceiling, wall or floor panels can also soundproofing a room. but To quiet a single machine or component, wrapping the entire room is not practical. In that case, creating an enclosure around the equipment and insulating the walls of that enclosure is the superior solution. The exact frequency of the sound also plays a factor. At 125 hertz (low engine noise), ½ inch of fiberglass can block about 5% while 2 inches of fiberglass can block about 25%. At 2000 hertz (high engine noise), ½ inch of fiberglass can block about 85%, while 2 inches of fiberglass blocks about 98%.
- Metal Buildings Are Difficult to Insulate to Code Even though the structures are far cheaper than wood construction, metal buildings have the drawback of being energy inefficient. Heat emits and conducts right through those thin layers of metal, whether it’s heat coming in during the summer or heat leaking out during the winter. ASHRAE 90.1 dictates the allowable heat transfer for a metal building (expressed in U-value) to meet building codes. In the 2012 version, the highest amount of heat transfer allowed is U-0.044. This is often achieved with R-19 fiberglass in the cavity between the purlins and R-11 continuous foam on the outside of the purlins, but a simpler solution using reflective insulation allows for all the insulation to fit nicely between and under purlins on the interior, without the need for external continuous foam insulation. Simply install R-19 fiberglass batts between the purlins like usual, and then apply a reflective insulation (usually aluminum or copper film laminated to bubble or flexible foam insulation) to the underside of the purlins. For aesthetic appeal, the downward facing surface can either be reflective or a while plastic film. The resulting heat transfer is U-0.042, a 5% improvement over the traditional insulation method.
- Radio Frequencies Can Interfere With Sensitive Electronics Bulk insulation is practically useless when protecting sensitive electronics from EMPs,or security Sensitive Compartment Information Facilities (SCIF) for military or other secure operations. For these applications, low-emissivity metals like aluminum, copper and gold are the best options with aluminum being the preferred material because it is widely available and has the lowest emissivity across the entire electromagnetic spectrum. The US Department of Defense recommends aluminum foil or aluminum vacuum deposited film products installed behind the gypsum board on all exterior walls for buildings requiring SCIF-level protection. However, if you just have a specific frequency you are more concerned with, aluminum may not necessarily be your best option. For example, at 100 MHz, which is near center in the radio spectrum, aluminum offers a resistance of just under 90 dB, while copper offers over 150 dB, so if you were only concerned with radio transmission, copper may be the better material.
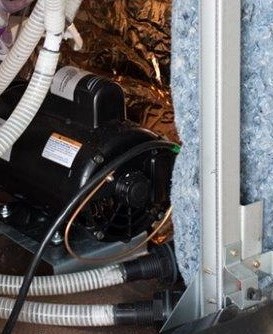
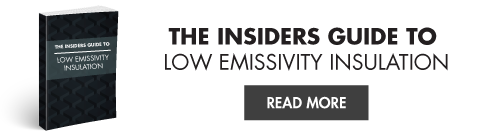
Reader Comments