Multi-Layer Insulation -- What Makes it Different
- Conduction -- where the heat transfers directly through a medium. This is how a frying pan works.
- Convection -- where a moving medium (like water or air) continuously brings colder medium in contact with a warmer surface. This is why wind chill makes air feel colder.
- Radiation -- where heat leaves an object in the form of electromagnetic (infrared) radiation. This is how the sun feels warm on your skin.
Different applications of insulation rely more heavily on one method of heat transfer than on others. Convection, for example, doesn’t exist in a vacuum so only conduction and radiation remain.
Multi-layer insulation spaces heat-reflective insulation material across air space. This minimizes conduction because of the space between layers, and each layer minimized radiation by reflecting back 95% to 98% of infrared radiation. Dozens of alternating layers combined create an incredibly efficient insulator, used everywhere from NASA space suits, to modern cryogenics, to textiles and building materials.

Each heat-reflective layer of a typical MLI product is a half-millimeter (0.0005 inches) thick polyester film, metallized with aluminum, copper, gold, or another metal. Spaces between the films most often consist of an open weave of fiberglass or ceramic threads. This permits production of highly insulative materials that still drape, ship and shape like fabrics. Other instances call for thin foils of aluminum, copper or gold, with the “crumple” of the foil layers being strong enough to sustain air space in vacuum.
NASA space suits, for example, require 12 alternating layers of heat-reflective films and conduction insulative air spaces. They allow astronauts to comfortably withstand temperatures from as cold as -250F to as hot as +450F -- increasing the range of tasks astronauts can perform, and places they can explore.
Cryogenics applications, which don’t need to give the insulated party as much mobility as a space suit -- may have an inch of MLI containing 60 layers. With temperature and vacuum control, these can achieve the equivalent of R-1440 (k value below 0.1 mW/m-K in vacuum). Energy for refrigeration is historically the highest cost in keeping a cryogenics operation running, so insulation this effective can mean achieving sustainable operating costs.
Residential construction, which isn't in a vacuum, also utilizes multi-layer insulation. In that application, the small air pockets in layers between the reflective films are resistant to air currents responsible for convection. The layers of heat-reflective film or foil increase the R-value of the air in those pockets. In construction, multi-layer reflective insulation systems either achieve a higher R-value for a more energy-efficient home, or allow an R-value that matches local codes in a smaller space.
For example, a 2 by 4 section of wall with fiberglass batting might have an R-value of 11 to 15, while 7 layers of aluminum foil subdividing the space achieves a total of R-18. A block wall, by contrast, would have only 1.5 inches of space for insulation as compared to the 3.5 inches in most stud walls. Owens Corning R-7 board comes in that thickness at approximately $1.00 per square foot. MLI products including Sigma’s 3100 Series and FiFoil’s VR Plus shield achieve R-4.5 to R-7.1 insulation for 10 to 20 cents per square foot. Contractors and developers don’t need to be told how valuable cutting insulation costs while using less space can be to their margins.
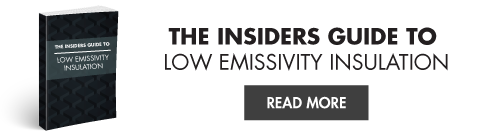
Reader Comments