The Importance of Testing Radiant Barrier
The primary performance characteristics, like surface emissivity, corrosion resistance, breathability and even the strength of radiant barriers can change, batch-to-batch and run-to-run during manufacturing. Products need to be tested and retested to make sure they are meeting spec, especially if you’re marketing or advertising a certain quality or performance.
In addition to emissivity of aluminum products changing over a long exposure to oxygen or water, the emissivity is also affected by the protective coating over the top (used to prevent corrosion over time) and the application of the coating, or even the metal itself, in the case of vacuum metalized products, can vary depending on the application. Additionally, the pins used to perforate products for breathability can dull over time, and must be periodically sharpened or replaced to maintain the radiant barrier’s breathability. Even the strength of the products can change depending on the quality and consistency of the internal reinforcement and the heat used in manufacturing. It’s important that manufacturers, resellers, distributors and even contractors be aware of the variation that can occur and have products periodically tested to ensure quality.
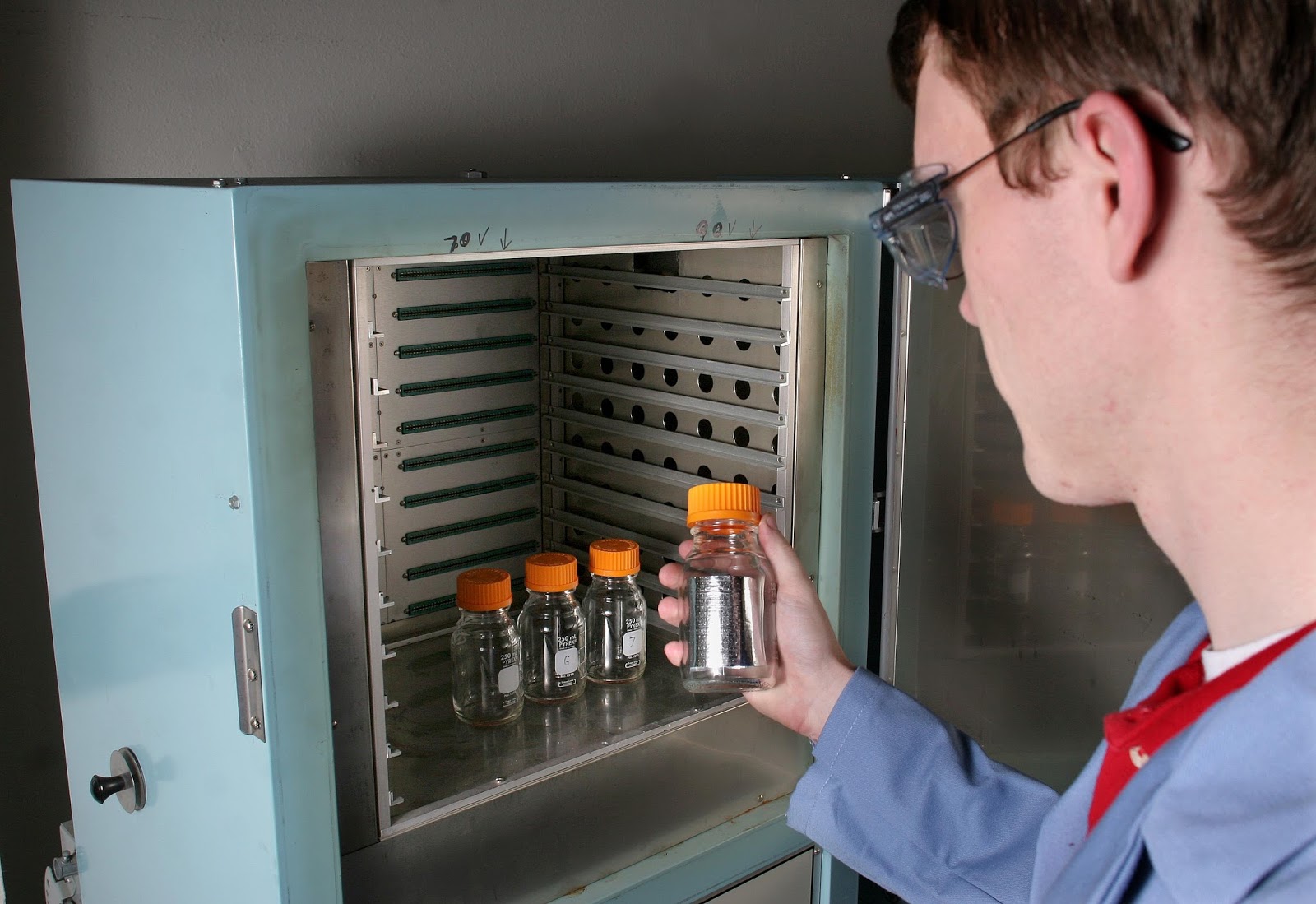
Some manufacturers are able to test performance characteristics of their radiant barriers in-house, and spot-check for quality, whereas others must send samples to outside labs. Doing it in-house requires specially trained staff to make sure the tests are being run correctly. While most of these tests are relatively easy to perform with practice, the user error of someone untrained on the equipment can lead to inaccurate results. Additionally, even relatively small testing equipment, like the Portable Emissometer or the Tensile Testing Machine can be very expensive to purchase (thousands of dollars), and relatively inexpensive to have tested by an outside lab (hundreds of dollars), so depending on the frequency of the quality checks, it may be more cost-effective to send samples out to a lab as needed.
In the case of ASTM tests, ASTM provides the contact information of testing labs certified to test to each standard, making it easy to get competing quotes. Sigma Technologies International is able to test every roll of radiant barrier they manufacturer, but they already have engineers on staff and own much of the testing equipment anyway since a significant part of Sigma’s business is making custom insulation, films and fabrics (both metalized and unmetalized) for large companies. Therefore, it isn’t a significant additional expense to have engineers test the radiant barrier prior to its packaging and shipping.

Another reason manufacturers, distributors, and installers may need to periodically test their radiant barrier is to keep records on file to back up claims made. As the Federal Trade Commission (FTC) lays out in its “R-value Rule”, any claims made on the performance of the insulation (like emissivity or R-value) must be backed up by testing data from no longer than 3 years from the date of the last claim. Specific states or municipalities may require a higher standard. The state of California, for example, requires data from no more than 1 year from the date of the claim. This means, even if you are 100% confident in the quality and consistency of the radiant barrier you sell, you must have recent performance data on record in order to advertise the performance of your radiant barrier.
Of course, any contractor or installer offering a warranty on the radiant barrier, on anything from the performance of the material itself and the savings the customer should expect, to the workmanship and quality of the installation, should have the performance characteristics of the product tested to avoid liability. While manufacturers, resellers and distributors sell the product for cents per square foot, contractors and installers make dollars per square foot, so warranty claims can be much more expensive. A product with a higher emissivity or a lower insulating value than advertised, or a product that is so weak that it is difficult to work with and properly install, may lead to a warranty claim.
While manufacturers in the US may be used to testing to ASTM, UL, and FTC standards, manufacturers overseas may not. Any distributors or resellers buying material from overseas may want to verify the quality of the material with each shipment. While attributes like strength may be easy to give a “pass or fail” without additional testing, some important attributes like breathability/permeability and reflectivity/emissivity are practically impossible to detect with the naked eye.
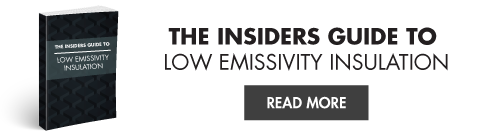
With emissivity, for example, products that are visually reflective may not be very reflective in the infrared, whereas products that look visually dull may still reflect very well in the infrared. Some manufacturers could put on too thick of a clear coating over the aluminum, resulting in a product that will hold up well to moisture, but may only be 50% emissive and 50% reflective. On the other hand, a manufacturer may put on too thin of a coating or neglect a coating all together, resulting in a product that is 3% emissive and 97% reflective, but corrodes quickly and easily, losing its performance, down to 35% emissive and 65% reflective. A radiant barrier should be no more than 10% emissive and no less than 90% reflective to meet the definition of a radiant barrier according to ASTM C1313.
Breathability or permeability is also hard to verify with the naked eye. Products with large perforations may actually be less permeable than products with smaller perforations, depending on the frequency and positioning of the perforations. Even the smallest change in the size of the holes due to the dulling of pins or the heat applied to the material (resulting in shrinkage of the plastic reinforcement) can reduce the breathability. Likewise, small variations like a shifting of the material going through the perforator, the height distance from the material to the perforator, the pressure of the pins, and even the speed of the perforator can affect the final breathability and permeability. ASTM E96 describes the test method for measure the perm rating of a product by measuring how much water vapor is able to pass through. ASTM C1313, the Standard Spec for Sheet Radiant Barrier, and ASTM C1224, the Standard Spec for Reflective Insulation set the acceptable standards for radiant barrier and reflective insulation products. A perm rating of greater than 5 is required for any product intended to be breathable, according to ASTM C1313 and ASTM C1224. If a manufacturer produces a product hovering above 5 perms, it would be wise to monitor the material periodically to ensure that it doesn’t fall to 5 perms or less at any point. While slight variations run-to-run or batch-to-batch may be less urgent for those companies with a higher perm product, it still may be wise to keep an eye on it over time.
There are many factors that go into producing, selling and installing radiant barrier products, and all of these performance characteristics can change. Attributes like emissivity, corrosion resistance, breathability, and strength, are essential for any radiant barrier product, and therefore, should be continually tested to make sure the radiant barrier is performing as it should.
Reader Comments